Next-Generation Nuclear Technologies for Decarbonizing Maritime Vessels
- Briggs McCriddle
- May 2
- 39 min read
International maritime commerce is the backbone of global trade, carrying over 80% of world merchandise by volume. However, this vital industry also produces significant greenhouse gas emissions—roughly 3% of global CO₂ emissions—comparable to the output of a major national economy. Decarbonizing the shipping sector is therefore critical for meeting international climate targets. Conventional cargo ships burn fossil fuels (heavy fuel oil or marine diesel), emitting CO₂, NOₓ, SOₓ, and particulate matter. Alternative propulsion methods such as liquefied natural gas (LNG), biofuels, hydrogen, ammonia, and battery-electric systems have been proposed, but each faces limitations in energy density, scalability, or infrastructure requirements. For instance, a large container ship requires on the order of 3,000 MWh of energy per day at sea—about the output of the world’s largest grid battery—making pure battery propulsion infeasible beyond short routes. Fuels like ammonia or hydrogen contain significantly lower energy per volume than diesel (ammonia has roughly half the energy density), necessitating roughly double the fuel volume and posing challenges for global fuel production capacity. Even with ambitious growth in renewable energy, producing hundreds of millions of tonnes of carbon-free ammonia or hydrogen for shipping would demand enormous resources, potentially competing with land-based energy needs. These constraints have led to a renewed interest in nuclear energy as a high-density, zero-carbon power source for ships.
Nuclear marine propulsion is not a new idea—over 700 reactor-years of experience have accumulated in naval vessels (submarines, aircraft carriers) and specialized civilian ships (icebreakers) operating reliably in harsh ocean environments. In the mid-20th century, a few experimental commercial nuclear ships were built, including the U.S. NS Savannah (launched 1959), Germany’s Otto Hahn (1968), Japan’s Mutsu (1970), and Russia’s Sevmorput (1988). These early projects demonstrated technical viability but were not economically successful, largely due to the reactor technologies of the time. NS Savannah’s pressurized-water reactor (PWR) proved complex and expensive to operate, contributing to the ship’s early deactivation by 1972. Similarly, Otto Hahn and Mutsu were converted to diesel propulsion after encountering operational and regulatory difficulties. Only Sevmorput remained in service into the 2020s, mainly serving niche Arctic routes under Russian operation. These experiences, under a vastly different economic and environmental context, stalled further development of nuclear commerce vessels for decades.
Today, the convergence of urgent climate imperatives and advanced nuclear technology is prompting a reevaluation of nuclear-powered shipping. Next-generation reactors—particularly small modular reactors (SMRs) employing Gen-IV designs—and the prospective advent of practical nuclear fusion promise fundamentally new capabilities. SMRs are compact and potentially simpler nuclear fission reactors, often designed with inherent and passive safety features, that could overcome the hurdles faced by earlier marine reactors. In parallel, progress in fusion energy research hints at the possibility, albeit longer-term, of fusion-powered ships with virtually limitless fuel and zero risk of meltdown. This article provides a scholarly analysis of how these next-generation nuclear technologies might be applied to cargo vessels for long-term service. We will (1) examine the technological aspects of integrating SMR and fusion systems into maritime settings, focusing on reactor design, safety, and development status; (2) review the global policy and regulatory framework for nuclear propulsion, including recent initiatives to update international codes; (3) evaluate economic feasibility, comparing costs and lifecycle economics with conventional and alternative fuels; (4) assess lifecycle emissions in a nuclear-propelled fleet versus traditional fuel cycles; and (5) discuss engineering integration challenges, supply chain considerations, and operational safety for nuclear-powered cargo ships. By drawing on current data and research (through 2024/2025), we aim to elucidate both the promise and the difficulties of nuclear energy at sea, providing an updated foundation for academic and industry discussion on the future of carbon-neutral shipping.
Technological Aspects of Nuclear Propulsion in Maritime Vessels
Small Modular Reactors (SMRs) for Marine Propulsion
Reactor Design and Compact Modular Integration: Modern small modular reactors are designed to deliver tens to a few hundred megawatts of thermal power in a compact form factor, making them suitable for installation in large ship hulls. Unlike the first-generation marine reactors (all based on pressurized light-water reactors), many next-generation SMRs use alternative cooling and fuel configurations that improve power density and safety. Notably, several designs have been identified as promising for ships: molten salt reactors (MSRs), lead-cooled fast reactors (LFRs), and high-temperature gas-cooled reactors using TRISO fuel. These systems can be made relatively small in size. For example, one proposed marine MSR design by UK-based Core Power would fit a 100 MW_th reactor in a 4×7 m footprint, a scale feasible for retrofitting into a merchant vessel’s engine room. Multiple SMR units could be used in one ship if needed to reach the desired power; a study by the American Bureau of Shipping (ABS) suggested that two 30 MW reactors could propel one of the world’s largest container ships with ample power. The modular nature of SMRs implies they could be factory-fabricated and then installed into ships during construction or major retrofits. This factory production can ensure quality control and potentially reduce costs compared to custom on-site construction, mirroring anticipated cost savings for land-based SMR deployment.
Passive Safety Systems: Next-generation marine reactors prioritize passive and inherent safety to mitigate the unique risks of operating in a mobile, remote environment. Unlike traditional PWRs that operate at high pressure and require active cooling, many advanced SMRs run at near-ambient pressure and rely on natural physical principles for emergency cooling and shutdown. This virtually eliminates the possibility of a high-pressure accident or boiler explosion. For instance, high-temperature gas reactors with TRISO fuel (tristructural isotropic fuel pellets) can withstand temperatures over 2000 °C without fuel failure, meaning even in a total loss-of-coolant scenario the fuel would not melt. In molten salt designs, the fuel is already in liquid form and mixed with coolant; if a leak or loss-of-flow occurs, the salt is designed to solidify as it cools, effectively trapping radioactive material in a solid matrix. This has been analogized to spilled molten caramel that hardens upon cooling, preventing any widespread contamination. Lead-cooled fast reactors similarly would have their liquid metal coolant solidify upon contact with seawater, sealing in the core and stopping fission reactions in an accident. All these Gen-IV marine reactor concepts are “walk-away safe,” meaning they do not require active intervention or powered systems to remain safe in emergency conditions. The reactor designs include features such as negative temperature coefficients (reactivity drops as temperature rises), passive heat removal by natural circulation, and fail-safe shutdown systems. These characteristics are critical at sea, where crew might need to evacuate in an extreme event; the reactor must stabilize itself without external support. Furthermore, an Emergency Planning Zone (EPZ) – the radius around a reactor within which special emergency plans are required – can be minimized. The goal for advanced marine reactors is to confine the EPZ entirely within the ship’s hull, meaning that even in worst-case scenarios, radiation exposure outside the vessel would remain below regulatory limits. Achieving a minimal EPZ is pivotal for commercial viability, as it would enable nuclear ships to enter ports without imposing emergency planning on port cities.
Maritime Suitability and Performance: SMRs must be engineered to function reliably under maritime conditions, including constant motion (pitching, rolling, wave impacts) and variable loads. The NuProShip consortium in Norway (a collaboration of maritime authorities, shipbuilders, and universities) has been evaluating candidate reactor technologies explicitly for their seakeeping tolerance. Designs that use liquid fuel or coolant (MSR, LFR) inherently dampen some reactivity fluctuations, whereas solid-fuel reactors must ensure coolant flow is not disrupted by motion. Structural support and mounting of the reactor system are designed to withstand shocks and vibrations. On the performance side, nuclear reactors offer essentially unlimited range and high power density. A nuclear-powered cargo vessel does not carry thousands of tonnes of combustible fuel; instead, a relatively small mass of nuclear fuel (on the order of a few tons of uranium or thorium) can provide energy for many years. This frees up cargo space and weight that would otherwise be allocated to bunker fuel. In fact, the ABS study found that installing two 30 MW LFR units could increase cargo capacity and even improve ship speed, since the weight and volume of reactors plus shielding were less penalizing than the enormous fuel bunkers and engines they replace. A well-designed 30–100 MW-class marine SMR could propel a large container ship at 20+ knots, matching conventional engines, with no refueling required for potentially 20–30 years of operation. This long refueling interval (or even full lifetime core) is a key advantage — by avoiding frequent refueling, operational logistics are simplified and security risks in port are reduced. For example, Russia’s Sevmorput operates with a single refuel for decades, and future designs plan for no refueling over a 25-year lifespan.
Current Development Status: As of 2024, there is significant momentum in developing marine-capable SMRs. International consortia and companies are actively pursuing designs. Norway’s NuProShip program has shortlisted three Gen-IV reactor concepts (MSR, LFR, and high-temperature gas) and aims to select a design by end of 2024 for prototyping. South Korea launched a project with shipbuilders and the national atomic energy research institute (KAERI) to develop and demonstrate SMR-powered ships, leveraging the country’s strong shipbuilding industry. In Japan, major shipyards (e.g. Imabari) have invested in UK-based Core Power, which is working on a 100 MW MSR for maritime use. Italy’s Fincantieri and the startup Newcleo (developer of a lead-cooled fast reactor) are conducting a joint feasibility study on integrating a 30 MW reactor into a vessel. Additionally, the United States Department of Energy, via the ABS, concluded a study in 2023 identifying candidate advanced reactors for merchant ships and R&D gaps that need addressing. These efforts indicate a broad recognition that suitable reactor technology is on the horizon. Demonstration timelines vary, but a rough consensus is emerging that the first next-generation nuclear commercial vessel could launch in the early to mid-2030s. Notably, proving these reactors on land (e.g. in stationary power or floating power plant applications) is seen as a prerequisite to maritime deployment. Russia already operates a floating nuclear power plant (the Akademik Lomonosov, with two 35 MW PWR-based SMRs) and China and South Korea are developing similar offshore nuclear barge projects. These will build operational experience with compact reactors in marine environments (though not propelling ships), helping validate safety and performance before propulsion use. In summary, the technological foundation for SMR-powered ships is rapidly solidifying, with multiple reactor designs approaching readiness for marine demonstration in the next decade.
Nuclear Fusion Systems for Maritime Use
Prospective Fusion Marine Reactors: Nuclear fusion, the process powering the sun, promises an ultimate long-term solution for ship propulsion: essentially limitless fuel (deuterium from seawater, lithium to breed tritium) and zero greenhouse emissions or long-lived radioactive waste. A fusion reactor would generate energy by fusing light nuclei (typically deuterium and tritium), producing helium and releasing immense heat which can be used to drive turbines or other propulsion mechanisms. Fusion has inherent safety advantages over fission: there is no risk of meltdown or runaway chain reaction (the reaction can only occur under precise controlled conditions and stops if any parameter drifts out of range), and the fuel is not weapons-grade. For maritime applications, a fusion power plant could be an attractive “holy grail” – “a compact, lightweight and inexhaustible energy source to power large ships across the seven seas” . Researchers have begun to contemplate what a shipboard fusion reactor would entail. A recent conceptual design study (van Rheenen et al., 2024) examined the feasibility of installing one of the smallest projected magnetic-confinement fusion reactors – the ARC design (a compact tokamak concept developed at MIT, ~200 MWe output) – into a large ship. The study targeted the Queen Mary 2 cruise ship as a reference, as it is one of the few commercial vessels with power demands (on the order of 100+ MWe) approaching the ARC’s output.
Technical Challenges and Development Horizon: The findings of that study and others indicate that significant hurdles remain before fusion propulsion is practicable. Even a “compact” fusion device like ARC is physically large and heavy due to the required superconducting magnets, shielding, and support systems (vacuum chamber, cryogenics, tritium handling). Fitting such a reactor in a hull without severely compromising ship design (stability, space, and weight distribution) is non-trivial. Vibration and motion could affect delicate plasma confinement. Moreover, ARC’s ~200 MW output is actually far higher than needed for most single ships, raising the issue of what to do with excess power or how to throttle a fusion reactor efficiently at part-load. Overall, van Rheenen et al. conclude that “a fusion reactor onboard a ship is unlikely to be feasible in the near future”, and that it may take several decades before marine propulsion can benefit from fusion. This assessment aligns with the general state of fusion: as of 2025, no fusion plant has yet produced net electricity. Nonetheless, progress is accelerating. Several private companies and public projects aim to demonstrate net-positive fusion energy by the 2030s. If these efforts succeed, the subsequent step would be commercialization on land (grid power stations). Only after fusion is mature and compact enough for terrestrial use would adaptation to ships become conceivable. In the interim, one indirect pathway to leverage fusion for shipping is using land-based fusion (or fission) plants to generate synthetic fuels (like hydrogen or ammonia) for ships – effectively using fusion energy without putting the reactor onboard.
Fusion-Powered Ship Concepts: Despite the challenges, some future-looking studies present optimistic scenarios for fusion in shipping. A notable example is a concept outlined by Det Norske Veritas (DNV) in its 2021 Energy Transition Outlook, envisioning a “fusion-powered container vessel” (FPCV) in service by mid-century. In DNV’s concept, a fusion reactor (likely a tokamak or stellarator) is housed in a sealed engine room, providing heat to steam generators and turbo-electric propulsion. The design retains a conventional layout (heat exchangers, steam turbines, generators, then electric motors driving the propellers) but swaps the combustion boiler for a fusion core. The increased engine room size slightly reduces cargo capacity, but the ship would gain in performance: higher sustained speeds and no need for refueling stops, except for periodic maintenance . Economic modeling in that report suggested that after an initial period, fusion-powered vessels could achieve lower total costs than conventional ships. Under reasonable fuel price growth scenarios, a fleet of fusion container ships was projected to break even within about 5 years and save on the order of $1 billion after 15 years compared to oil-fueled equivalents. These savings come from avoided fuel costs and potentially faster delivery times (as nuclear ships could maintain higher speeds without concern for fuel consumption). The DNV report concluded that “the fusion-powered container vessel offers potential for lower transport cost, faster service and zero emissions to air, [removing] business uncertainty due to fuel cost volatility”, positioning fusion as a promising long-term (post-2040) option for global shipping. While such projections are speculative, they underscore the appeal of fusion if key technological breakthroughs occur. In summary, practical fusion reactors for ships remain a futuristic prospect, but ongoing advancements merit keeping this option in view for the latter half of the 21st century. In the nearer term, advanced fission SMRs are the more actionable technology for nuclear marine propulsion, with fusion representing a potential successor once matured.
Global Policy and Regulatory Frameworks
The deployment of nuclear propulsion in civilian cargo vessels is as much a regulatory and political challenge as a technical one. Historically, stringent regulations and liability concerns have been primary barriers to nuclear commercial ships. Any nuclear-powered ship must navigate a complex web of international maritime law, nuclear safety standards, and port access protocols. This section examines the current frameworks and recent developments in policy governing nuclear ships.
International Maritime Organization (IMO) Regulations: The IMO adopted a “Code of Safety for Nuclear Merchant Ships” in 1981 (IMO Resolution A.491(XII)), which is incorporated as Chapter VIII of the SOLAS (Safety of Life at Sea) Convention. This code was written in an era when only pressurized-water reactors were envisioned, and it provides technical guidelines and requirements specifically for PWR-based ship reactors with direct steam turbines. The 1981 code addressed reactor containment, safety systems, and emergency planning, but its scope is narrow and predicated on assumptions from first-generation reactor technology. In particular, because a mobile high-pressure reactor could potentially have a significant Emergency Planning Zone extending beyond the ship, the code effectively assumes such ships cannot be easily accommodated in ports. As a result, no comprehensive update has been made in over four decades, and the code is now widely seen as outdated. It does not account for advances like passive-safe SMRs or alternative reactor coolants (liquid metal, molten salt, etc.), and thus it lacks provisions for licensing Gen-IV reactors on ships. Recognizing this gap, IMO member states have in recent years begun discussions to modernize the nuclear ship code. In 2025, IMO’s Maritime Safety Committee (MSC) was scheduled to discuss revising the SOLAS nuclear provisions to create a more flexible, technology-neutral framework. A Correspondence Group on GHG Safe Shipping has identified specific regulatory gaps hindering advanced nuclear integration and has recommended aligning the code with current IAEA safety standards. The aim is to enable new reactor types while upholding safety. Proposed updates include performance-based safety requirements applicable to any reactor design that meets certain risk thresholds, rather than prescriptive rules assuming a PWR. If adopted, these revisions would mark a significant step toward enabling SMR-powered commercial ships under international law, by providing clear guidelines for their design approval, operation, and inspection.
National Regulations and Port Access: Beyond the IMO’s international standards, each flag state (the country of registry of a vessel) and port state (countries where the vessel visits) can impose additional requirements. One major hurdle is that many nations currently have laws or policies effectively barring nuclear-propelled civilian vessels from their ports, often due to public concern or the lack of an agreed liability framework. For example, after incidents like the Mutsu (which suffered a minor radiation leak in 1974), public opposition in Japan to nuclear ships grew, and ports refused entry, forcing early decommissioning of that program. In the U.S., any commercial nuclear ship would require licensing by the U.S. Nuclear Regulatory Commission (NRC) in addition to maritime authorities, adding layers of regulatory review. The ABS-led study noted that fragmented regulation is a concern: a reactor design approved in one jurisdiction isn’t automatically accepted elsewhere. This is analogous to how nuclear power plants on land are licensed country by country. To address this, efforts are underway in international forums (including G7 nations and the International Atomic Energy Agency) to harmonize nuclear regulatory requirements across borders for marine reactors. Harmonization would allow a ship reactor design to be certified to a common standard (or mutually recognized standards), easing its approval in multiple countries. Another regulatory barrier is export control. In countries with naval reactor programs (e.g. USA, UK, Russia, China, France), naval nuclear technology is highly classified and subject to strict export controls. There is a concern that any marine reactor technology might be swept under the same restrictions, impeding international collaboration or sales. Mikal Bøe (2024) notes that export control rules need to distinguish clearly between military naval reactors and civilian maritime reactors to allow the latter’s development and transfer. The civilian designs emphasize proliferation resistance (e.g. using low-enriched fuel, sealed reactors, or fuel not suitable for weapons) to allay security concerns. Indeed, Gen-IV designs being considered have features like fuel self-expended over life or use of thorium-233U cycles that are unattractive for weaponization, supporting a case for relaxed export restrictions in the civilian context.
Liability and Insurance: One of the thorniest policy issues is liability for nuclear incidents at sea. Existing international nuclear liability conventions (the Vienna and Paris Conventions) were not formulated with moving reactors in mind and explicitly exclude nuclear-powered ships from their coverage. An attempt to craft a dedicated framework, the Brussels Convention on the Liability of Operators of Nuclear Ships (1962), failed to achieve ratification and effect, largely because at the time there was no political consensus on how to insure or attribute liability for a nuclear ship accident. Without a liability regime, commercial insurers have been unwilling to insure nuclear vessels, and countries have been unwilling to accept them in port due to the risk of unaddressed legal claims in case of an accident. This stands in contrast to naval vessels, where governments self-insure and assume liability. The emergence of inherently safer reactors could change this calculus. If it can be demonstrated that an advanced reactor has a negligible risk of off-ship impact (due to the minimal EPZ and “no release” safety case), then insurance could become commercially viable. Industry advocates argue for a new liability convention tailored to modern nuclear ships, which would set reasonable liability limits and compensation mechanisms, thereby giving insurers and port authorities confidence to allow nuclear vessels. Some proposals suggest that the ship’s flag state or the reactor vendor might take on a defined liability and carry a financial security (much like oil tankers carry insurance for oil spill liability under MARPOL conventions). Progress on this front is nascent, but it is recognized as a key enabler: without resolution of liability and insurance, nuclear shipping will not be commercially feasible. As of 2024, the discussion is gaining momentum along with the technical advances. The European Union’s classification of nuclear energy as part of its sustainable finance taxonomy (with caveats) hints at a more favorable policy environment, and European maritime safety agencies (e.g. EMSA) are actively studying pathways to include nuclear in shipping’s decarbonization toolkit.
Safety and Security Governance: Operating reactors on merchant ships demands a rigorous safety culture and security safeguards. International safeguards (to prevent proliferation) would need to cover enriched fuel loaded in ships, likely under IAEA monitoring if nuclear fuel is transferred across borders. From a safety governance perspective, classification societies (such as ABS, Lloyd’s Register, DNV) are preparing rules for nuclear propulsion. ABS has already released guidance that begins to address design and arrangement questions for shipboard reactors. Issues such as crew training and certification are being discussed: officers might require specialized qualifications analogous to naval nuclear operators or civilian reactor operators. Security against unauthorized access or terrorism is also a concern; proposals include designing the reactor as a “black box” module that is difficult to tamper with and locating it deep within the ship’s protected zones. Some advanced designs contemplate sealed reactors that would never be opened in port – the entire reactor module would be replaced at end of life, and spent fuel processing would occur only in secure facilities on land. This approach aligns with the criterion of avoiding any refueling or fuel handling in ordinary ports, as identified by policy experts. In summary, the governance framework for nuclear shipping is in flux, with active efforts to update international codes, harmonize regulations, and devise insurance solutions. The coming few years (mid-2020s) are likely to be decisive in setting the enabling regulatory environment that will either unlock or stifle the potential of nuclear-powered commercial vessels.
Economic Feasibility and Lifecycle Cost Analysis
A critical question for the adoption of nuclear-powered cargo vessels is whether they can be economically competitive over their lifetime compared to ships using conventional or other alternative fuels. This section evaluates the capital and operating costs, fuel cycle economics, and overall feasibility from a financial perspective, drawing on recent studies and data.
Capital Costs (CAPEX): Nuclear ships require a substantially higher initial investment than diesel-fueled ships of equivalent size. The reactor itself is a major capital item, as are associated systems (shielding, secondary steam plant, control systems) and the specialized engineering of the vessel’s nuclear island. Historical examples illustrate the premium: NS Savannah in the late 1950s cost US$46.9 million to build (around $0.5 billion in today’s dollars), far more than a conventional ship of its class . Modern SMR-based designs still carry a high price tag due to the novel technology and stringent quality requirements. While exact figures are proprietary or in development, one estimate for a 70 MW ship SMR could be on the order of a few hundred million USD, potentially several times the cost of a marine diesel engine system. Additional capital costs include crew training facilities, licensing costs, and nuclear-specific infrastructure at shipyards. Furthermore, financing costs for a nuclear vessel might be higher due to investor risk perceptions. However, there are mitigating factors. If SMRs for ships can be mass-produced, economies of series production could significantly drive down unit costs. Standardization and a high volume of identical reactors (for a fleet of ships) could follow models from the aerospace or automotive industry rather than one-off custom builds. Some analyses suggest that with sufficient scale, the cost of a nuclear propulsion system could approach parity with the escalating costs of new alternative-fuel engines (e.g. dual-fuel LNG engines, or fuel cell systems) plus their fuel storage. A European Maritime Safety Agency (EMSA) study in 2024 reported that initial techno-economic models show the total cost of ownership (TCO) of an SMR-powered ship can be comparable to that of a conventional fuel ship at present, and likely advantageous in future scenarios. The TCO includes CAPEX plus operating costs over the life. The EMSA report noted that while nuclear has higher upfront CAPEX, this may be offset by fuel and carbon savings over time, especially as conventional fuel costs rise under carbon pricing regimes. Key to reducing nuclear CAPEX will be advancements in reactor design (simplifying systems, modular construction) and favorable financing (perhaps government-backed loans or inclusion in green financing initiatives, now that nuclear is classified as sustainable in some jurisdictions).
Operating Costs (OPEX) and Fuel Cycle: Operating a nuclear-powered cargo ship would incur a very different cost structure from a conventional ship. The most striking difference is fuel cost. A large container ship today might burn on the order of 100-150 tonnes of fuel oil per day at sea; at a fuel price of, say, $600 per tonne, that's $60,000–$90,000 per day in fuel expense. Nuclear fuel for an equivalent output is orders of magnitude more energy-dense. A 100 MW reactor running 24/7 might consume only a few kilograms of uranium or thorium fuel per day. In terms of raw fuel, the cost is trivial – a kilogram of low-enriched uranium (LEU) fuel might produce as much energy as many tons of oil. Over a 25-year core life, the total fuel cost (uranium, enrichment, fabrication) for a ship’s reactor could be perhaps a few million dollars, which is negligible compared to the tens of millions per year a similar diesel ship spends on bunker fuel. Thus, nuclear offers a huge potential OPEX saving: one analysis estimated an MSR-powered ship could save about $70 million in fuel costs over its lifetime relative to a diesel-fueled ship. Additionally, nuclear fuel prices are relatively stable and decoupled from oil market volatility, reducing uncertainty in operating costs. However, other operating costs for nuclear ships are higher. These include costs for the nuclear-qualified crew (likely more engineers with specialized training and higher salaries), ongoing reactor monitoring and maintenance, periodic safety inspections, and regulatory compliance (e.g. fees for licensing, insurance premiums if available, security measures). Maintenance of the reactor and associated systems is complex; every few years the ship might require downtime for in-depth inspection or servicing of the reactor, which could mean hiring specialist teams or returning to certain shipyards equipped for nuclear work. Some SMR concepts aim to minimize onboard maintenance by encapsulating the core such that it only needs service at long intervals (e.g. replacement of the module at 20+ years). If no refueling is required during the ship’s normal life, operational logistics simplify greatly, essentially limiting nuclear maintenance to the same schedule as a major overhaul or dry-docking. The ABS study posited that a large nuclear ship would not need to refuel over 25 years, aligning reactor servicing with end-of-life decommissioning. Decommissioning and waste disposal are another lifecycle cost: at the end of service, the reactor will have to be removed and dealt with as radioactive waste (unless it’s refueled and the ship’s life extended). The ship owner would need to account for the cost of reactor dismantling or returning the module to the supplier. In some economic models, a “residual value” for the spent reactor might be assumed if the reactor still contains usable fuel or if governments provide a take-back program for SMR modules. Nonetheless, prudently a decommissioning fund would be set aside, as done for nuclear power plants.
Competitiveness under Different Energy Scenarios: The economic viability of nuclear propulsion improves in scenarios where conventional fuel prices are high or where stringent carbon taxes/levies are imposed on fossil fuels. At present, marine fuel prices fluctuate with oil markets and have been trending upward also due to new low-sulfur fuel requirements. Moreover, the International Maritime Organization has adopted measures to reduce carbon intensity of shipping and is discussing market-based measures (like carbon pricing per tonne of CO₂). If, for example, a carbon levy of $100 per tonne CO₂ were applied, this could add on the order of $300 per tonne to the cost of bunker fuel (since each tonne of fuel oil emits ~3 tonnes of CO₂). Such a policy would dramatically widen the OPEX gap in favor of nuclear, which emits no CO₂ and would not incur the levy. According to the EMSA 2024 study, rising carbon costs could indeed make conventional fuels “less competitive over time, increasing the gap in OPEX” between nuclear and oil. On the other hand, nuclear’s competitiveness could be challenged by certain alternative fuels if they become cheap and abundant – for instance, if green ammonia or methanol production scales up and their costs drop, those could provide a zero-carbon fuel solution without nuclear’s regulatory overhead. However, as discussed earlier, scaling those fuels to global shipping demand appears highly challenging and they may remain costly. There is also the option of nuclear-assisted synthetic fuels: using onshore nuclear (fission or fusion) to produce hydrogen-based fuels. This effectively transfers the cost from the ship to shore infrastructure. Some argue this might be more practical in the near term, but it introduces its own inefficiencies (energy conversion losses and handling costs of the synthetic fuel).
Macro-Economic and Strategic Factors: On a fleet level, nuclear propulsion could allow faster transit speeds and fewer stops (since refueling is not needed). In container shipping, faster delivery can be economically beneficial (higher asset turnover), though speed is often limited by fuel costs. If fuel cost is negligible, ships could save time by sailing 5–10 knots faster than today’s slow-steaming speeds, potentially reshaping logistics. One study suggested fusion-powered ships could sustainably travel at high speeds, improving service levels. There is also an opportunity cost benefit: eliminating large fuel tanks frees volume for revenue-generating cargo. For certain ship types (like LNG carriers), the volume taken by LNG tanks is enormous; a nuclear-powered LNG carrier could carry more payload instead of fuel. A 2023 ABS conceptual study found that cargo capacity actually increases when replacing a large fuel-oil powertrain with a nuclear unit on a very large container ship, as mentioned. Over the lifecycle, a nuclear ship might carry additional thousands of containers cumulatively, translating to more revenue. Balanced against these upsides are financial risks: regulatory changes or public opinion shifts could impose unexpected costs or even bar a nuclear ship from operation after construction (policy risk), and accidents (however unlikely) carry potentially huge liabilities. Investors and lenders may demand government guarantees or insurance pools to cover these contingencies, which effectively socializes some of the risk. Governments might be willing to support nuclear ships as part of climate strategy, similar to how some nations subsidize alternative fuel pilots. Indeed, projects in South Korea, Japan, and Europe have public co-funding for nuclear maritime R&D.
In conclusion, the economics of nuclear-powered cargo vessels appear increasingly promising in a carbon-constrained world. High capital costs remain a major barrier, but trends in fuel prices and carbon policy, combined with the possibility of modular mass-production, could narrow the gap. Preliminary analyses suggest that when considering full lifecycle costs (including fuel, operations, and eventual decommissioning), an SMR-powered ship can reach cost parity or better with conventional ships, especially beyond the initial years of operation. Moreover, intangible benefits like energy security (not relying on volatile oil markets) and faster transit could add to the value proposition. Still, to realize these economic advantages, non-economic barriers (regulation, public acceptance) must be overcome, and early movers will likely require policy support or niche mission profiles (such as high-endurance research or supply vessels) to justify the investment until economies of scale take hold.
Environmental and Emissions Considerations
A primary motivation for nuclear propulsion in shipping is the potential to drastically reduce harmful emissions. This section compares the lifecycle environmental impact of nuclear-powered ships to conventional fossil-fueled ships and other alternative propulsion options, focusing on greenhouse gases and air pollutants, as well as waste management.
Greenhouse Gas Emissions: Nuclear fission reactors emit effectively zero CO₂ during operation. A nuclear-powered cargo vessel would have no exhaust stack releasing CO₂ (or CO, HC, etc.), in stark contrast to a diesel engine burning heavy fuel oil. Over a single long voyage, a large container ship can emit thousands of tonnes of CO₂; a nuclear ship performing the same voyage would emit none from propulsion. On an industry scale, if a substantial portion of the world fleet converted to nuclear, the impact on global shipping emissions (approximately 3% of global CO₂) would be profound, essentially eliminating that share. The only greenhouse gas emissions attributable to a nuclear ship stem from its fuel cycle (mining and enriching uranium, manufacturing the reactor) and from construction and decommissioning. Studies indicate that the lifecycle carbon footprint of nuclear power (per kWh) is very low—comparable to wind power, and an order of magnitude lower than fossil fuels, even accounting for mining and plant construction. The EMSA report affirmed that nuclear energy has zero emissions during operation and low carbon intensity over its lifecycle. Thus, even when including upstream processes, a nuclear ship would vastly outperform a ship running on oil, LNG, or even synthetic carbon-based fuels in terms of lifecycle GHG emissions. One must note that alternative zero-carbon fuels like green ammonia or hydrogen fuel cells also have zero operational CO₂, but their lifecycle emissions depend on how they are produced. If produced with renewable or nuclear electricity, their lifecycle can be near-zero; if produced from fossil fuels with carbon capture, some upstream emissions remain. Nuclear's advantage is providing a direct power source without intermediate fuel conversion losses.
Air Pollutants (SOx, NOx, PM): In addition to CO₂, conventional ship engines emit sulfur oxides (SOx), nitrogen oxides (NOx), and particulate matter (PM), which contribute to air pollution, acid rain, and health problems especially around port cities and shipping lanes. Nuclear propulsion virtually eliminates these pollutants: there is no combustion, so no formation of SOx/NOx. The primary atmospheric discharge from a nuclear ship might be just water vapor (from the steam cycle condenser) and negligible coolant gases. This could substantially improve air quality impacts of shipping. The IMO’s 2020 sulfur cap (limiting fuel sulfur content to 0.5%) was implemented to reduce SOx from ships, either by using lower sulfur fuels or scrubbers. A nuclear ship inherently meets any future zero-emission standards for SOx and NOx. Similarly, nuclear ships would not produce black carbon (soot), which is a concern in the Arctic due to its ice-melt acceleration effect. Thus, widespread nuclear adoption could help address not only climate goals but also regional environmental quality goals.
Water and Marine Environment: One environmental aspect to consider is the cooling water discharge from nuclear ships. Reactors will likely use a secondary loop to transfer heat to seawater via a heat exchanger, resulting in warm water being discharged. The thermal pollution from a single ship is minimal compared to a coastal power plant, as the ship is moving and mixing its coolant discharge into the vast ocean. Still, near ports, procedures may be needed to avoid thermal impact if any. Nuclear ships must also safeguard against any radioactive release into the marine environment. Under normal operation, releases are essentially zero—modern reactors do not vent any radioactivity except perhaps minor noble gases under controlled conditions. The risk is in accident scenarios: if a reactor were severely damaged or if a ship sank. This could lead to localized contamination (as occurred with a few sunk nuclear submarines). Advanced reactor designs mitigate this risk: passive shutdown would occur before any explosive accident, and as noted, solidification of fuel/coolant can prevent dispersion. The reactor compartments can also be engineered to withstand sinking (e.g., pressure-proof and designed to contain the reactor even under water). International guidelines would likely require recovery of a sunken nuclear ship if feasible, to prevent long-term ocean contamination. Overall, the probability of a severe environmental release is extremely low with new designs, whereas the routine pollution from thousands of oil-fueled ships is a certainty that accumulates damage continuously.
Waste Management and Decommissioning: A full environmental assessment must include the nuclear waste generated. A shipboard reactor is typically smaller than a land power reactor, but after years of operation it will contain highly radioactive fission products in its fuel. The spent fuel (if removed) or the entire reactor module (if sealed) will need to be dealt with. This is a backend burden not present for conventional ships, which only produce CO₂ (diffused in the atmosphere) and engine scrap metal at end of life. The nuclear waste issue is not unique to maritime use; it is essentially the same challenge as for any SMR. The volume of spent fuel from a small reactor is modest – possibly on the order of a few cubic meters per core – and could be stored or reprocessed in existing facilities. Some advanced designs aim to consume their own long-lived actinides (if fast spectrum) or use thorium such that waste radio-toxicity is reduced. For example, Newcleo’s concept LFR would “recycle the by-products of conventional reactors, offering a circular solution to nuclear waste” , implying that a fleet of such reactors could help reduce overall nuclear waste stockpiles. Regardless, safe handling of spent fuel and possibly reactor disposal will require strict adherence to nuclear waste regulations. In lifecycle emissions accounting, the long-term storage of waste does not emit greenhouse gases, but it is an environmental responsibility extending beyond the ship’s operational life.
Comparison with Other Alternative Propulsion (Lifecycle): It is instructive to compare nuclear with other proposed zero-carbon shipping solutions on a lifecycle basis:
Batteries: If a ship were to use batteries charged from renewable energy, operational emissions would be zero, but manufacturing huge batteries has a significant environmental footprint (mining of lithium, etc.), and the weight of batteries reduces efficiency. For deep-sea routes, batteries are impractical as noted, due to enormous weight/volume needs. Nuclear can achieve zero emissions without that weight penalty.
Hydrogen Fuel Cells: A hydrogen fuel cell ship would emit only water vapor. But producing hydrogen is energy-intensive; if using renewables, large-scale hydrogen production may indirectly require more mining (for solar panels, etc.) and has conversion losses. Also, hydrogen storage on ships (cryogenic or high-pressure) is volume-inefficient and poses safety risks (flammability). Ammonia as a carrier avoids CO₂ but introduces NOx and toxicity issues if leaked.
Wind-Assisted and Synthetic Fuels: Retrofits like rotor sails can cut some fuel use (and emissions) but cannot fully propel large ships. Synthetic carbon-neutral fuels (like e-methanol) still emit CO₂ at the exhaust but ideally that CO₂ was captured earlier – however, the capture and synthesis processes have energy losses. The nuclear route essentially uses on-board energy generation, circumventing those losses and intermediate emissions.
In terms of climate impact, nuclear is one of the few options that can truly eliminate tank-to-wake emissions (emissions from the ship itself) and drastically reduce well-to-wake (full fuel lifecycle) emissions for shipping. The trade-off is introducing radioactive materials into the maritime environment, which necessitates robust safety management. Given the existential importance of decarbonizing shipping, many experts now argue that the environmental benefits of nuclear outweigh the risks, provided modern reactors are used. Jan Emblemsvåg, a professor leading a maritime nuclear project, stated that considering the scale of shipping’s decarbonization challenge, “for commercial shippers, there aren’t any realistic alternatives to nuclear” when it comes to achieving zero emissions at the required power levels. This underscores the view that from an emissions standpoint, nuclear is uniquely positioned to meet the long-term needs of a sustainable shipping industry.
Engineering Integration, Supply Chain, and Operational Safety
Implementing nuclear propulsion on cargo ships entails overcoming numerous engineering and logistical challenges beyond the reactor technology itself. This section discusses how a reactor would be integrated into a ship’s design, the supply chain requirements (fuel, components, expertise) for building and operating nuclear ships, and the operational safety considerations including crew training and emergency procedures.
Ship Design Integration: The naval architecture of a nuclear-powered merchant ship must accommodate the reactor and its support systems in the hull without compromising the vessel’s primary function of carrying cargo. Typically, the reactor would be situated low in the ship (likely near midships for stability), within a heavily shielded compartment. This compartment would resemble a small nuclear power plant containment, adapted to ship structure. Critical considerations include:
(1) Shielding and Radiation Protection: Thick radiation shielding (lead, steel, or concrete composites) is required around the reactor to ensure radiation in crew and cargo areas is negligible. This adds weight, but designers aim to optimize placement of heavy components to maintain stability. For instance, the reactor and shielding can double as ballast if positioned properly.
(2) Thermal Integration: The reactor’s heat must be transferred to either a steam turbine or another conversion system (possibly a closed Brayton cycle for some gas reactors). Most likely, steam turbines driving generators or directly driving a propeller via reduction gears will be used, as this is proven in naval practice. Thus, a secondary loop with steam generators, condensers, feed pumps, etc., is needed. This essentially recreates a power plant engine room, and indeed the engine room of a nuclear ship will be larger than a diesel engine room. In modern concepts, the reactor produces electricity (via a turbine-generator) which then powers electric propulsion motors. This provides flexibility in placement (reactor doesn’t have to be aligned with propeller shaft) and is consistent with trends toward electric drive in large ships (e.g., cruise ships and LNG carriers often use electric azimuth thrusters).
(3) Cooling Systems: The ocean provides an infinite heat sink for reactor cooling, which is a benefit — cooling water will be drawn from the sea to condense steam or cool a secondary fluid. Emergency cooling may involve natural circulation of seawater through a heat exchanger if pumps fail. One advantage of a ship is that it can use the surrounding water for passive heat removal in a loss-of-power situation, as long as some part of the ship is submerged. Designs might include hull penetrations for heat exchangers that work by convection.
(4) Containment of Radioactive Materials: The reactor compartment would be sealed and designed to contain any release. Even in a severe internal accident, radioactive steam or gas should not vent to the environment. This may involve a double-hull structure around the reactor compartment to act as a secondary containment. The goal of a self-contained EPZ (emergency zone) within the hull has been noted, meaning the ship itself houses the safety perimeter.
(5) Structural and Stability Impacts: The weight of a reactor and shielding is significant (potentially a couple of thousand tons), which is comparable to or perhaps somewhat more than a fully fueled conventional engine room. Ship designers must ensure proper weight distribution. Intact and damage stability need to account for the dense mass of the reactor—if the ship takes on water or lists, the reactor’s position should not lead to capsize. Usually, this is managed by placing the mass low and central. The structure around the reactor might be reinforced to protect against collisions or grounding damage. A collision at the reactor area is extremely unlikely if placed near center and below waterline, but designers consider even oblique scenarios. The ABS study answered naval architects’ questions on arrangement: the consensus was that a reactor can be fit without eating up all cargo space or making the vessel unrecognizable, although precise designs are still being developed.
Fuel Supply Chain: Operating nuclear ships will require a robust supply chain for nuclear fuel. Most proposed marine reactors would use low-enriched uranium fuel (LEU, <20% U-235) or possibly thorium with uranium or plutonium seeds. Enriched fuel is not as readily available as bunker fuel; it is produced by a limited number of facilities worldwide under tight regulations. A fleet of nuclear ships implies a demand for dozens or hundreds of SMR cores over time. This could be a new market for the nuclear fuel industry. Enrichment capacity might need expansion, though compared to the needs of nuclear power plants, the total uranium demand for a fleet of ships is not huge (a single large land reactor of 1 GWe uses as much fuel as perhaps 10–20 ship reactors of 50 MW each). One strategy is to utilize existing fuel fabrication for research reactors or SMRs, which typically supply high-assay LEU fuel. For instance, TRISO fuel (for high-temperature gas reactors) or certain metal alloys (for fast reactors) are being manufactured in pilot scales now; scaling up would be necessary. International safeguards and transport regulations govern how nuclear fuel is moved — fresh LEU fuel is radiologically not very dangerous (only mildly radioactive), but it is sensitive material. Likely, fueling of ships will occur at designated secure ports or naval shipyards. Perhaps a ship’s reactor is fueled at the country of construction and then not refueled until end of life or mid-life at a specialized facility. This means the commercial fuel supply chain will involve coordination between reactor vendors and shipping companies for take-back and refueling services. The mention from policy experts is clear: “no need for refueling of reactors in commercial ports” is a desired criterion. Fuel would thus be inserted and removed only at specialized locations (e.g., at a reactor supplier’s site or a naval base), not during routine operations. This can be planned to coincide with dry-dock intervals. If life-of-ship cores become viable, then the supply chain challenge simplifies to delivering fresh fueled reactors to shipyards and receiving the spent ones decades later. Thorium fuel cycles could also be employed in MSRs; thorium is more abundant and not proliferation-sensitive, but it requires breeding U-233 and is still experimental. Some countries might favor designs that use their domestic fuel resources or align with their nuclear regulatory framework. For example, a country without domestic enrichment might hesitate unless assured of fuel supply from abroad. International cooperation (perhaps IAEA fuel bank schemes) could support nuclear marine fuel availability.
Manufacturing and Shipbuilding Infrastructure: Only a limited number of shipyards worldwide have experience with nuclear vessel construction (largely military yards in the US, UK, France, Russia, etc., and some in China). For nuclear merchant ships to become common, civilian yards in major shipbuilding nations (South Korea, China, Japan, Europe) will need to develop the capability to install reactors. This may involve partnerships between nuclear reactor companies and shipbuilders. Indeed, we see such partnerships forming: e.g., South Korea’s Hyundai Heavy Industries with its nuclear division, Japan’s Imabari with Core Power, Italy’s Fincantieri with Newcleo. Initially, reactor modules might be built entirely at a nuclear supplier’s factory and shipped to the yard for insertion. Shipyards will have to implement nuclear quality assurance standards, train workers for nuclear assembly tasks, and coordinate with nuclear regulators. This is a non-trivial shift; however, once a yard has a certified process, it could become a leader in a new niche of high-value “nuclear ready” ships. There may also be a need for specialized support vessels or facilities, such as a service ship that can carry a replacement reactor module to a vessel at sea or assist in an emergency (analogous to naval submarine tenders). The broader supply chain includes maintenance contractors, waste handling companies, and regulatory bodies, all of which must scale up.
Operational Safety and Crew Training: Safe operation of a nuclear ship requires a well-trained crew and a rigorous safety management system. The crew would include Nuclear Engineers or Reactor Operators on board, likely with similar training to naval reactor operators or commercial reactor operators. Maritime academies may introduce nuclear propulsion in their curriculum. There would also need to be shore-based support: an operations center with reactor experts monitoring fleet reactor data 24/7, to assist crews and respond to any anomalies (similar to how the nuclear navy operates with continuous shore support). Emergency procedures will be detailed and practiced: although the design aims to make emergencies highly unlikely, crews must know how to shut down the reactor (if not already scrammed automatically), cool it, and contain any issues. Unlike a land plant, evacuation in case of serious trouble might mean the crew takes to lifeboats – hence the insistence on passive safety that does not require human intervention. Drills would also involve coordination with port authorities for emergency response, though if EPZ is within hull, port evacuation might not be needed even for a severe incident. Nonetheless, the ship’s flag state will likely require an emergency response plan approved by nuclear authorities. Security is another operational aspect: nuclear fuel and the reactor must be protected against theft, sabotage, or misuse. This could mean armed security onboard, especially when in port or high-risk areas, and strict control of access to the reactor compartment. Insider threat mitigation (screening crew) and cybersecurity for reactor control systems are also important. The reactor control systems would be designed to fail-safe and be isolated from external interference (likely not connected to the internet, for example). If a ship were hijacked by pirates, the reactor should ideally be able to be shut down remotely or be inherently safe from causing harm. These scenarios, while very unlikely, have to be considered in risk assessments.
Emergency Response and International Collaboration: In the event of an incident at sea (say a reactor malfunction, or damage from grounding), assistance may be needed from specialized teams. An international framework might be established for maritime nuclear emergency response, perhaps leveraging IAEA’s response network and naval resources. Coastal nations would want notification if a nuclear ship in their waters has a problem. Transparent incident communication protocols will build trust that this new class of ships is being operated responsibly. The maritime industry can draw lessons from the nuclear navy, which has had accidents (such as the sinking of submarines) and managed responses. For example, after the sinking of the Russian K-278 Komsomolets submarine in 1989, measures were taken to contain leakage from the reactor. Preventative design like having the reactor scram and flood with a neutron absorber upon sensing certain shocks can reduce post-accident risks.
In summary, integrating a nuclear reactor into a cargo ship is a complex engineering task, but no insurmountable scientific barriers exist. It is more a matter of careful design and adherence to high safety standards. The supply chain to support nuclear shipping will require expansion of nuclear fuel fabrication and the marrying of nuclear and maritime industries. Operational safety will hinge on thorough training, failsafe design, and strong safety culture. As Patrick Ryan of ABS highlighted in industry discussions, there were many practical questions from shipbuilders: “Where does the crew go? What are the special training requirements? How do I insert this technology? How do I refuel?” . These questions are being addressed one by one through studies and early projects, and thus far no fundamental show-stoppers have been identified—only challenges that require prudent engineering and regulatory solutions. With each challenge addressed (be it a motion tolerance issue or a licensing process), the concept of nuclear cargo ships moves closer to reality.
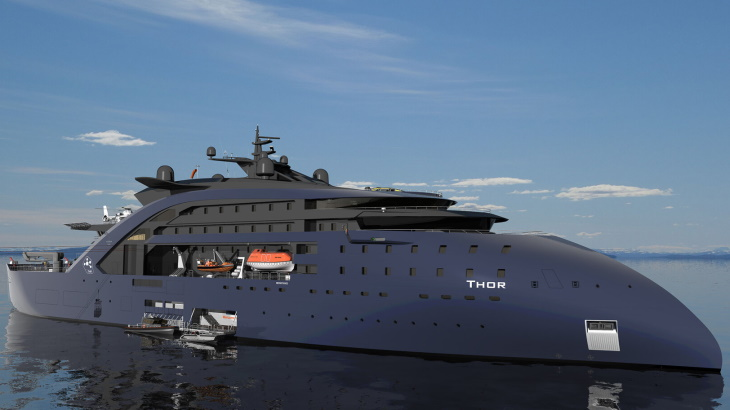
Figure 1: Artist’s concept of a future nuclear-powered vessel (Ulstein “Thor” concept with a molten salt reactor). Such designs incorporate a compact reactor in the hull and could serve as charging hubs for other ships, illustrating one vision of nuclear technology application in maritime settings.
Discussion and Outlook
The analysis above illustrates that next-generation nuclear technologies hold great promise for transforming the maritime industry by enabling zero-emission long-endurance propulsion. Small modular reactors, with their compact size and advanced safety features, are nearing the point of practical implementation on large vessels. Prototype deployments in the 2030s appear likely, given the confluence of technological readiness (several marine-reactor designs reaching maturity) and regulatory momentum (IMO and national bodies updating rules to accommodate nuclear). If these pilot projects demonstrate success in real-world conditions, a broader rollout could follow in the 2040s, aligning with global decarbonization timelines. The use case of nuclear propulsion is especially compelling for the largest and most energy-intensive ships—such as ultra-large container ships, bulk carriers on long routes, and icebreaking cargo vessels—where alternative solutions fall short. These vessels could be the first to justify the higher capital investment thanks to their high fuel use and the critical need for range and power.
Nuclear fusion, while not a near-term solution, remains an exciting prospect on the horizon. Should fusion energy reach commercialization mid-century, maritime adoption might follow in subsequent decades. Fusion-powered ships would likely first emerge in specialized roles or in nations that heavily invest in fusion technology. The timeline is speculative, but given the rapid progress in fusion experiments and private ventures, it is not beyond imagination that by the latter half of the 21st century, a handful of fusion-electric ships could be in operation, essentially running on seawater fuel and producing no pollution. In the meantime, the pursuit of fusion for shipping provides a useful impetus for addressing extreme engineering challenges (like containing a reactor in a moving platform) and could spin-off innovations that benefit fission reactor shipping as well.
Despite the optimism, several caveats are warranted. Public acceptance of nuclear ships will be a determining factor. One accident, however minor, could set back progress significantly by undermining confidence. Transparency, rigorous safety demonstration, and effective communication will be needed to assure the public and stakeholders (such as ports and seafarers’ unions) that nuclear-propelled vessels can be as safe as (or safer than) conventional ships. The example of nuclear naval vessels, which have operated for decades with very few incidents, is a strong precedent, but military operations are less visible to the public than commercial operations would be. Hence, the first movers may involve government-owned or -backed vessels (for example, state-run shipping lines or special-purpose ships for research or humanitarian supply) to blaze the trail and prove the concept in the civilian world.
Another discussion point is the alternative role of nuclear in shipping: instead of putting reactors on every ship, some propose using large floating reactors or nuclear-powered tankers to produce clean fuels (hydrogen, ammonia, synthetic methane) that can be bunkered by other ships. This “indirect” use of nuclear could circumvent some regulatory hurdles (since the reactors stay in one place or in a fixed facility) and still decarbonize shipping fuel. For example, a fleet of nuclear-powered floating barges could station at strategic points producing ammonia from seawater and nitrogen, and tankers would distribute it. However, this approach introduces additional energy conversion losses and may be less economically efficient than direct nuclear propulsion, essentially shifting the problem rather than simplifying it. It could also be an interim step: using nuclear-generated fuels in the near term, and transitioning to onboard reactors in the longer term.
From a policy perspective, the coming years are pivotal. If the IMO and IAEA succeed in updating the nuclear ship code and creating frameworks for licensing and liability, the door will open for serious commercial ventures. We have seen shipping alliances form to test hydrogen, methanol, and ammonia; similarly, we may see a consortium order the first new-build nuclear cargo ship for pilot operation. This could happen in a controlled environment (e.g. serving a single dedicated route or region where ports agree to accept it). The Arctic trade or specific long-haul routes where ports are carefully chosen might be early candidates. Over time, as the ecosystem matures (suppliers, training institutions, insurance products, etc.), nuclear propulsion could capture a significant niche of the shipping market—particularly for routes where refueling is impractical or where environmental regulations are tightest (such as in emission control areas or sensitive regions).
There are also implications for global power and competition. Countries that pioneer nuclear merchant ships might gain a strategic advantage in green shipping. For instance, South Korea’s initiative to design an SMR-powered container ship could set it up as a leader in offering zero-carbon shipping services and capture market share from competitors who rely on costly carbon-neutral fuels. Likewise, Russia’s experience with nuclear icebreakers gives it a head start for Arctic cargo capabilities. International collaboration will be needed to ensure safety and non-proliferation are maintained as more actors enter the field of maritime nuclear propulsion.
In conclusion, the application of next-generation nuclear technology to cargo vessels is moving from theoretical possibility to actionable plan. The technical analysis increasingly supports viability: SMRs can be made safe and compact enough, and even offer performance benefits. The economics, under realistic future scenarios, tend toward favorable, especially factoring in carbon constraints. The regulatory and societal aspects, historically the toughest barriers, are beginning to be addressed through concerted efforts by industry, governments, and international agencies. While challenges remain, they appear surmountable with careful, interdisciplinary effort. Thus, nuclear-powered cargo ships may well become a cornerstone of sustainable global trade in the mid-21st century, marrying the energy density of the atom with the efficiency of modern shipping to achieve unprecedented range, speed, and environmental performance.
Conclusion
The drive to decarbonize maritime transport has brought nuclear propulsion back to the fore as a compelling solution for cargo vessels. This article has examined in depth the facets of deploying small modular reactors and, eventually, fusion reactors on ships. Technologically, modern nuclear reactors offer the necessary compactness, power output, and safety through passive systems to be viable at sea, overcoming many drawbacks of earlier naval reactors. The global regulatory regime is adapting, with efforts to update outdated rules and create pathways for licensing and insuring nuclear ships – developments essential for enabling commercial projects. Economically, although the initial investment is high, the total cost of ownership can be competitive, especially as conventional fuel costs rise with carbon pricing; nuclear propulsion promises operational savings, immunity from fuel price volatility, and potentially greater operational efficiency (faster voyages and larger cargo capacity). Environmentally, nuclear-powered ships would virtually eliminate the direct emissions of greenhouse gases and air pollutants from shipping, representing a radical reduction in the sector’s environmental footprint and helping meet global climate goals.
Significant challenges remain in engineering integration, from reactor installation to establishing a reliable fuel supply chain and ensuring absolute safety in operations. However, none of these challenges are deemed insurmountable in light of current research and experience. Pilot programs underway in several countries indicate that the first generation of SMR-propelled vessels could set sail within the next decade. Their performance and acceptance will likely determine the pace of broader adoption. If successful, we can anticipate a progressive rollout: nuclear propulsion might start with niche applications (icebreaking cargo ships, naval auxiliaries, or ultra-long-haul routes) and then expand to more general merchant fleets. In parallel, continued advancement in fusion energy may eventually yield an even more advanced class of ship propulsion, complementing fission SMRs or replacing them in the very long term.
In summary, next-generation nuclear technologies present a transformative opportunity for long-term, sustainable propulsion of cargo ships. They address the dual imperatives of dramatically reducing emissions and ensuring efficient, reliable transport for global trade. Realizing this vision will require not only technological innovation but also forward-thinking policy, industry collaboration, and public trust. As the world’s oceans have always been pathways for human progress, so too could they become the proving ground for a new era of clean energy, with nuclear-powered vessels charting the course toward zero-carbon shipping.
References
IEEE Spectrum (2024) – J. W. Walters, "The Case for Nuclear Cargo Ships," IEEE Spectrum, Updated 22 Jan 2024. (Insights into emerging SMR designs for ships, industry initiatives, and statements from experts on nuclear shipping) (The Case for Nuclear Cargo Ships - IEEE Spectrum)
IEEE Spectrum (2024) – Ibid. Further details on historical nuclear merchant ships and economic comparisons by J. Emblemsvåg (NTNU) regarding molten salt reactors vs. diesel. (The Case for Nuclear Cargo Ships - IEEE Spectrum)
IEEE Spectrum (2024) – Ibid. Discussion on alternatives (battery, ammonia) and rationale for nuclear, as well as technical overview of Gen-IV reactor options considered by NuProShip. (The Case for Nuclear Cargo Ships - IEEE Spectrum)
IEEE Spectrum (2024) – Ibid. Comments on safety features of advanced reactors (molten salt solidification analogy, lead coolant behavior) and results of an ABS concept study (two 30 MW reactors on a large container ship). (The Case for Nuclear Cargo Ships - IEEE Spectrum)
IEEE Spectrum (2024) – Ibid. Coverage of alternative approach (using nuclear to produce fuels vs. onboard reactors), challenges like port acceptance and public perception, and regulatory oversight (ABS, US NRC). (The Case for Nuclear Cargo Ships - IEEE Spectrum)
IEEE Spectrum (2024) – Ibid. Timeline for prototyping (NuProShip aiming for ~2030s), example of Ulstein’s "Thor" MSR-powered concept vessel as a charging station, and mention of regulatory harmonization efforts by G7/IAEA. (The Case for Nuclear Cargo Ships - IEEE Spectrum)
Ship & Bunker News (2025) – "IMO to Discuss Updating Safety Rules for Nuclear Ships," 28 April 2025. (Noting that IMO’s MSC 110 meeting in June 2025 will consider revisions to the 1981 Nuclear Ship Code to accommodate advanced reactors) (IMO to Discuss Updating Safety Rules for Nuclear Ships - Ship & Bunker)
World Nuclear News (2024) – M. Bøe, "Viewpoint: Modernising the regulatory ecosystem for nuclear-powered ships," 14 May 2024. (Analysis of regulatory gaps: SOLAS Chapter VIII limitations, export controls, liability conventions, and criteria for new nuclear tech in shipping) (Viewpoint: Modernising the regulatory ecosystem for nuclear-powered ships - World Nuclear News)
World Nuclear News (2024) – Ibid. Emphasizing the need for minimal Emergency Planning Zone within the hull, no refueling in ports, and passive safety as key criteria for new designs. (Viewpoint: Modernising the regulatory ecosystem for nuclear-powered ships - World Nuclear News)
Fusion Industry Association (2021) – "New Report Proposes Fusion-Powered Shipping," summary of DNV’s 2021 Energy Transition Outlook. (Concept of a fusion-powered container vessel, cost-benefit projection showing long-term cost savings and zero emissions) (New Report Proposes Fusion-Powered Shipping - Fusion Industry Association)
van Rheenen et al. (2024) – "Nuclear fusion as unlimited power source for ships," Proc. International Marine Design Conference 2024. (Investigation of integrating an ARC fusion reactor on a ship; concludes fusion is not feasible in the near future for marine propulsion due to size and other issues) ( Nuclear fusion as unlimited power source for ships | International Marine Design Conference )
SWZ Maritime / EMSA (2024) – G. Kramer, "EMSA study explores nuclear power for shipping," SWZ Maritime, 23 Dec 2024. (Summary of a European Maritime Safety Agency study on nuclear propulsion: Gen-IV reactor suitability, fuel availability, TCO analysis showing nuclear vs VLSFO parity, and CAPEX/OPEX trade-offs) (EMSA study explores nuclear power for shipping | SWZ)
World Nuclear News (2022) – "Ulstein touts nuclear concept for decarbonising cruise ships," 29 April 2022. (Description of Ulstein’s Thor concept vessel with a thorium MSR, serving as a floating power station for battery-electric cruise ships, illustrating innovative use-cases for maritime SMRs) (Nuclear vessel 'could be floating charging station for electric cruise ships' - World Nuclear News)
Comments